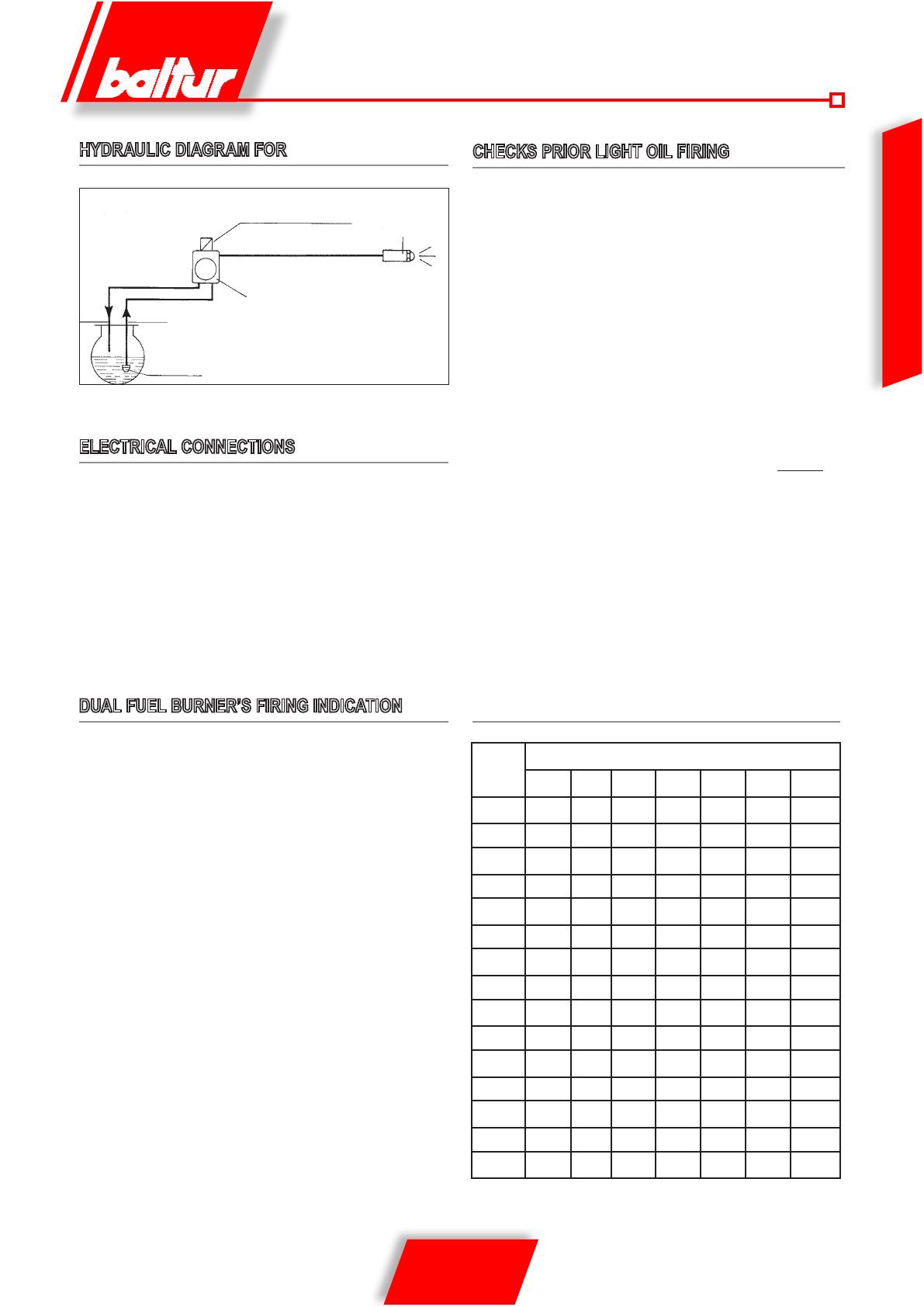
E
N
G
L
I
S
H
11 / 18
0006081159_201102
HYDRAULIC DIAGRAM FOR
8502cmt18.tif
Light oil electrovalve
Nozzle
Light oil pump
(12 bar pressure)
Return
Suction
Foot valve
ELECTRICAL CONNECTIONS
Electric lines should be at an adequate distance from
hot parts. Make sure that all electrical connections are
made with ex electric wire, with suitable size for the
voltage and absorbed power.
Maximum current absorbed = 600 VA
Minimum section of the feed line = 1mm
2
with 230V.
For the LGB 22 control box, the intensity of the cell
current should be between 200 microamperes and 500
microamperes.
DUAL FUEL BURNER’S FIRING INDICATION
We suggest to start the burner with the liquid fuel, as in this case
the delivery is bound to the nozzle size whilst the gas delivery can
be easily changed by acting on the relative capacity adjuster.
If the burner is in the automatic version, the selector for the fuel
change connects a cyclic relay which inserts, tanks to an auxiliary
relay, components for the use of both fuels (valves, pressure
switches, pump etc.).
After having changed the position of the selector from gas to light oil
and voiceovers, it occurs to leave it stopped for at least 10 seconds
which is the time the cyclic relay needs to carry out its program.
ATTENTION
If the selector is moved from a position to another before the period
of 10 seconds, the cyclic relay stops in the middle of its program not
allowing to use the burner both with gas and with light oil.
Nozzle
G.P.H.
Pump pressure bar
8 9 10 11 12 13 14
0,60 2,04 2,16 2,28 2,39 2,50 2,60 2,70
0,65 2,21 2,34 2,47 2,59 2,71 2,82 2,92
0,75 2,55 2,70 2,85 2,99 3,12 3,25 3,37
0,85 2,89 3,06 3,23 3,39 3,54 3,68 3,82
1,00 3,40 3,61 3,80 3,99 4,16 4,33 4,50
1,10 3,74 3,97 4,18 4,38 4,58 4,77 4,95
1,20 4,08 4,33 4,56 4,78 5,00 5,20 5,40
1,25 4,25 4,50 4,75 5,00 5,20 5,40 5,60
1,35 4,59 4,87 5,13 5,38 5,62 5,85 6,07
1,50 5,10 5,41 5,70 5,90 6,24 6,50 6,75
1,65 5,61 5,95 6,27 6,58 6,87 7,15 7,42
1,75 5,95 6,31 6,65 6,98 7,29 7,58 7,87
2,00 6,80 7,21 7,60 7,97 8,33 8,67 8,99
2,25 7,65 8,15 8,55 8,97 9,37 9,75 10,12
2,50 8,50 9,01 9,50 9,97 10,41 10,83 11,24
CHECKS PRIOR LIGHT OIL FIRING
Make sure that the nozzle with sprouting angle at 60° is suitable to
the boiler’s capacity.
In the list hereunder you nd the delivery values in kg/h of light oil
related to the nozzle’s size and to the pump’s pressure (normally
12 bar). (Please note that 1 light oil kg corresponds to 10.200
kcal about).
Make sure that the protrusion of the combustion head inside
the combustion chamber is according to boiler manufacturer’s
instructions.
Make sure that the return pipe in tank has no obstructions, such as
gates closed caps etc.
Probable obstructions could cause faults on the pump’s shaft or
ex pipe.
Open slightly the air purge device of the pump.
Disconnect the wire number 39 which feeds the pump motor from
the terminal on the contactor “K1” and connect it from moment the
terminal “K1.56” of the “input junction box” so as to feed directly
the pump motor.
Now close the reverser-switch on the burner and the general one
and make sure that the rotation sense is correct. Thus the pump
motor is connected and starts the pump witch sucks the light oil.
When the light oil ow the air purge device open the main switch
so as to stop the motor.
Be set original connections to the corresponding terminals.
The burner is thus ready to operate at light oil.
TABLE OF NOZZLE DELIVERY RATES IN Kg/h OF LIGHT
OIL