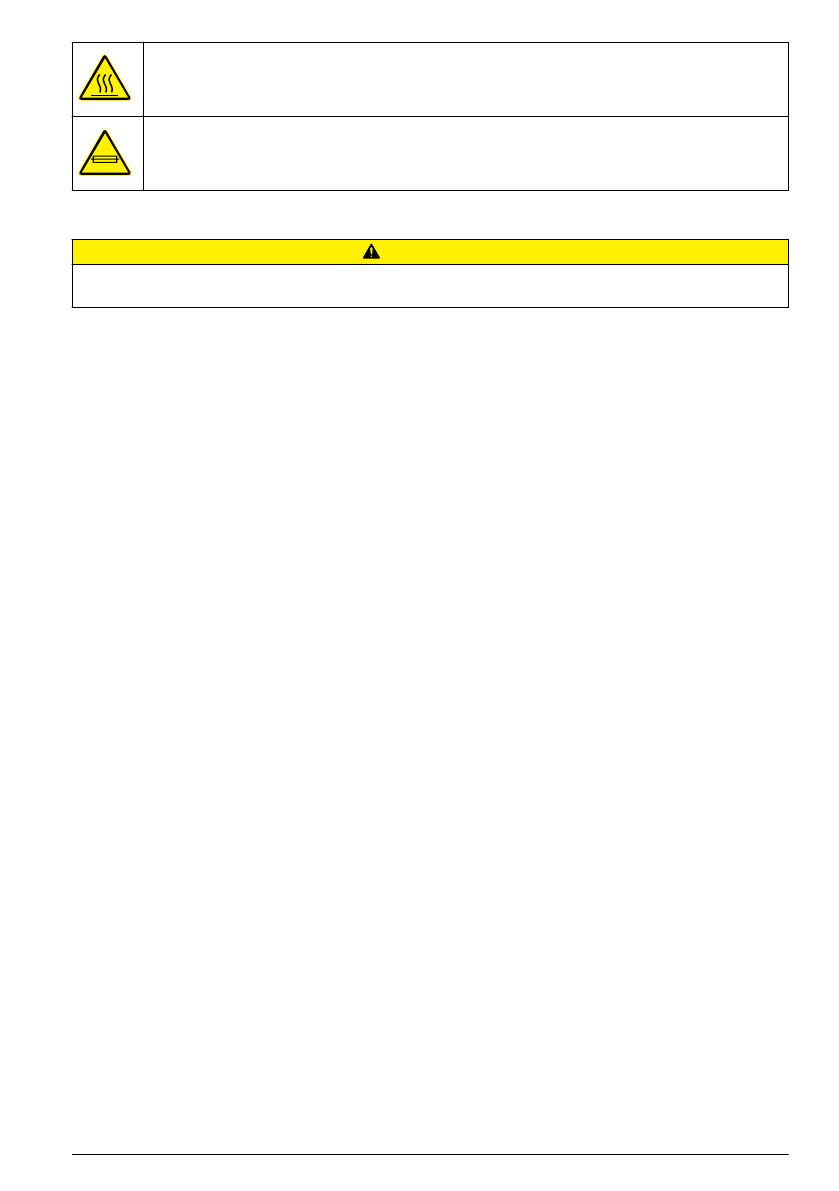
This symbol indicates that the marked item can be hot and should not be touched without care.
This symbol, when noted on the product, identifies the location of a fuse or current limiting device.
3.1.3 Certification
C A U T I O N
This equipment is not intended for use in residential environments and may not provide adequate protection to
radio reception in such environments.
Canadian Radio Interference-Causing Equipment Regulation, IECS-003, Class A:
Supporting test records reside with the manufacturer.
This Class A digital apparatus meets all requirements of the Canadian Interference-Causing
Equipment Regulations.
Cet appareil numérique de classe A répond à toutes les exigences de la réglementation canadienne
sur les équipements provoquant des interférences.
FCC Part 15, Class "A" Limits
Supporting test records reside with the manufacturer. The device complies with Part 15 of the FCC
Rules. Operation is subject to the following conditions:
1. The equipment may not cause harmful interference.
2. The equipment must accept any interference received, including interference that may cause
undesired operation.
Changes or modifications to this equipment not expressly approved by the party responsible for
compliance could void the user's authority to operate the equipment. This equipment has been tested
and found to comply with the limits for a Class A digital device, pursuant to Part 15 of the FCC rules.
These limits are designed to provide reasonable protection against harmful interference when the
equipment is operated in a commercial environment. This equipment generates, uses and can
radiate radio frequency energy and, if not installed and used in accordance with the instruction
manual, may cause harmful interference to radio communications. Operation of this equipment in a
residential area is likely to cause harmful interference, in which case the user will be required to
correct the interference at their expense. The following techniques can be used to reduce
interference problems:
1. Disconnect the equipment from its power source to verify that it is or is not the source of the
interference.
2. If the equipment is connected to the same outlet as the device experiencing interference, connect
the equipment to a different outlet.
3. Move the equipment away from the device receiving the interference.
4. Reposition the receiving antenna for the device receiving the interference.
5. Try combinations of the above.
3.2 Product overview
The 9525sc degas system removes CO
2
and measures degassed conductivity from the sample
stream. The 9525sc degas system boils the sample and distills the liquid through the crossover
system to remove CO
2
gas from the sample stream. The unit removes CO
2
gas through the steam
vent, and distills the flow through the sample cooler. The unit then measures the conductivity of the
sample.
Use the 9523sc cation conductivity panel to measure specific, cation and degassed conductivity. The
combined system is known as the 9525sc degas cation conductivity (DCCP) system. Refer to
English
5